Tensile Strength vs. Yield Strength [+Key Differences Explained]
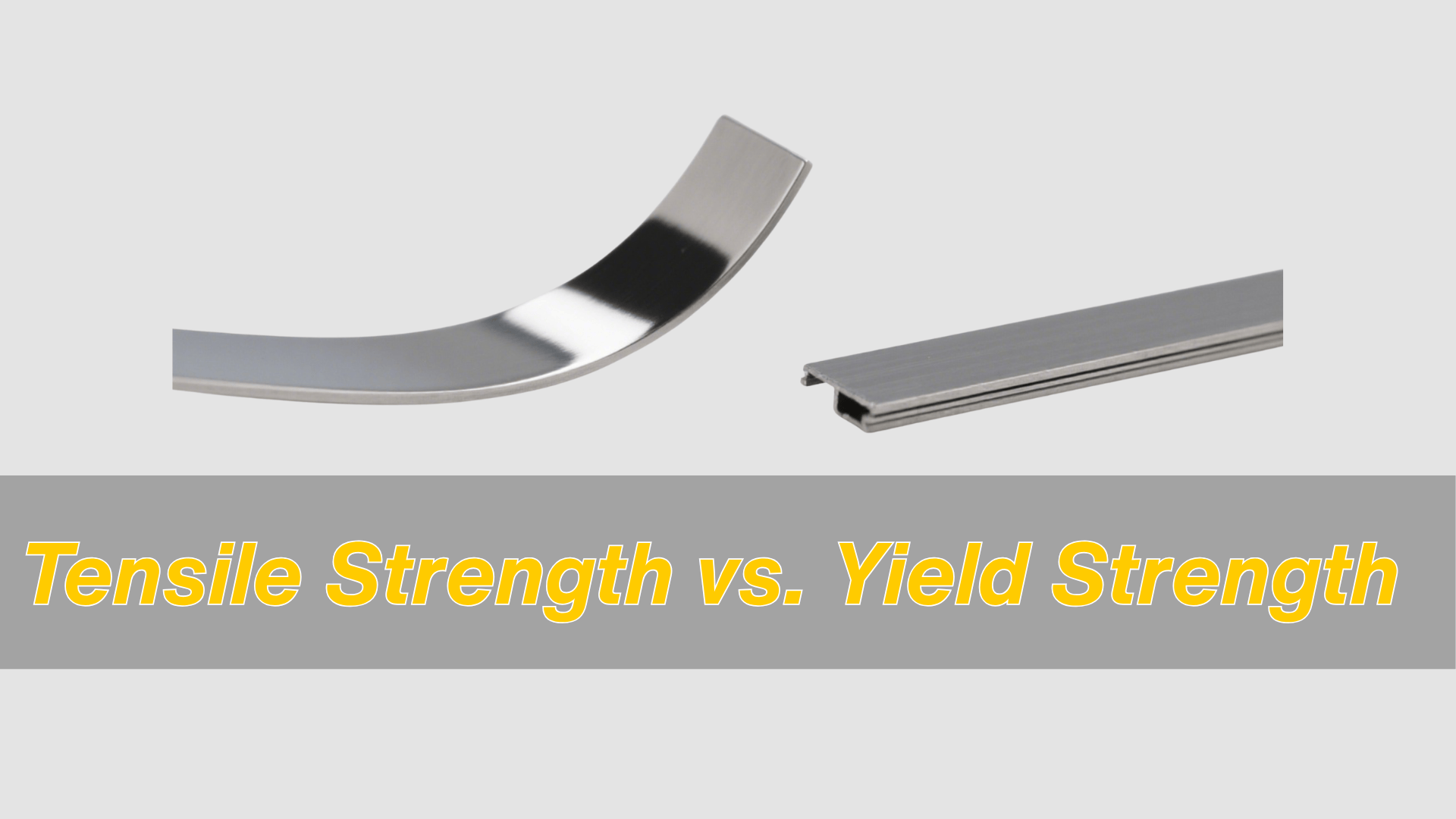
Understand the key differences between tensile and yield strength in 3D printing—design stronger, safer parts with the right mechanical insights.
Introduction
In 3D printing, choosing the right material goes beyond color or surface finish—it requires a deep understanding of how a material behaves under load.
Two key mechanical properties that often come up in design and engineering decisions are tensile strength and yield strength. Though they’re closely related, these properties determine how your 3D printed part performs under stress, how much it can bend before it breaks, and whether it will deform permanently during use.
This guide explains what tensile and yield strength are, how they differ, and why both are essential when designing and selecting materials for 3D printed parts.
What is Tensile Strength
Tensile strength, also named ultimate tensile strength(UTS), refers to the maximum stress a 3D printed material can endure when stretched before it ultimately breaks. It’s the material’s breaking point under a pulling force.
Unit: MPa (megapascals) or psi
Testing: Measured via tensile testing using ASTM D638 or ISO 527 standard dog-bone samples
Where it matters: Parts under continuous tension or subject to pulling forces—like load hooks, cable ties, snap-fits, and living hinges
Example: An FDM-printed part using carbon-fiber-reinforced nylon may have a tensile strength of 70–100 MPa, meaning it can handle significant tension before failing.
What is Yield Strength
Yield strength is the stress level at which a 3D printed material starts to undergo permanent deformation—even if the load is removed. Below this point, deformation is elastic and reversible.
Unit: MPa or psi
Significance: Defines the material’s functional limit—beyond this, the part will bend, warp, or sag and not return to its original shape
Where it matters: Load-bearing structural parts, enclosures, brackets, and mechanical joints
Example: A PLA part may have a yield strength of 50 MPa. Any functional load above this will cause bending or warping that doesn’t recover.
Yield Strength vs Tensile Strength: Key Differences
In 3D printing, both yield strength and tensile strength describe how a material behaves under pulling forces—but they represent different stages of mechanical stress.
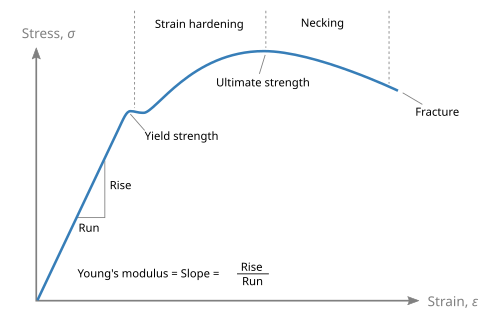
In One Sentence, yield Strength is the point where permanent deformation begins; Tensile Strength is the maximum stress a material can withstand before breaking.
Imagine stretching a paperclip:
When you stretch it slightly and it returns to its original shape → that’s within the yield strength.
When you keep pulling until it’s about to snap → that’s approaching the tensile strength.
Comparison Table:
Dimension | Yield Strength | Tensile Strength |
---|---|---|
Definition | Stress at which a material begins to deform plastically | Maximum stress a material can withstand before breaking |
Also Known As | Yield Point | Ultimate Tensile Strength (UTS) |
Position on Stress-Strain Curve | Marks the end of the elastic region | The peak point of the curve |
Deformation Behavior | Beyond this point, deformation is permanent | Occurs after significant plastic deformation, right before fracture |
Indicates... | Start of material's failure to maintain shape | Material's maximum strength before rupture |
Value Comparison | Always lower than tensile strength | Always higher than yield strength |
Reversibility | Deformation reversible before this point | No reversibility beyond this point |
Engineering Use | Used for design limits, safety margins | Used to assess overall strength, failure thresholds |
Material Dependency | Varies significantly among materials | Less variable in ratio, but absolute values depend on material type |
In Summary:
Use yield strength to prevent deformation during normal use.
Use tensile strength to ensure survival under extreme or accidental loading.
Typically, yield strength is always lower than tensile strength.
To learn more details about yield strength, read our previous article before: https://www.unionfab.com/blog/2024/03/yield-strength-of-steel
Application Significance of Yield Strength vs Tensile Strength
Understanding the application relevance of both yield strength and tensile strength is essential when designing functional 3D printed parts—especially when strength, durability, and safety matter.
Yield Strength: Designing Within Safe Limits
What it means: Yield strength marks the stress limit a 3D printed part can endure without permanent deformation.
Why it matters: In real-world use, most parts are designed to function without visibly bending or warping.
Example: A 3D printed bracket made of PETG used to hold a sensor—if forces exceed the yield point, the bracket may sag and misalign the sensor even if it doesn’t break.
Design Implication: Always keep operational stresses below the yield strength to ensure dimensional accuracy and reliable performance.
Tensile Strength: Preparing for Extreme Loads
What it means: Tensile strength is the maximum stress the part can take before it fractures completely.
Why it matters: This is a safety boundary—important for parts that may occasionally face unexpected overload.
Example: A flexible snap-fit clip may function well below yield but must survive occasional overextension without breaking.
Design Implication: Tensile strength provides a safety factor when designing for accidental misuse, drop, or overload.
Application-Specific Considerations
Application Type | Prioritize Yield Strength | Prioritize Tensile Strength |
---|---|---|
Mounting brackets, housings | Prevent long-term warping | / |
Snap-fit joints, flexible clips | Maintain shape with stress | Avoid snapping under stress |
Structural load-bearing arms | Design for sustained loads | Account for overload conditions |
Decorative or display-only parts | / | — (Mechanical strength less critical) |
In short:
Yield strength guides day-to-day functional reliability.
Tensile strength protects against rare but catastrophic failures.
Yield Strength vs Tensile Strength in Structural Safety
When it comes to structural safety, both yield strength and tensile strength play crucial but distinct roles in ensuring that 3D printed parts perform reliably under stress without sudden failure.
Yield Strength: The Threshold of Safe Use
Role in Safety: Yield strength defines the maximum stress a material or part can endure without permanent deformation.
Why it matters in structural safety: Parts designed with loads below their yield strength maintain their shape and function, avoiding deformation that can compromise assembly fit or mechanical performance.
In 3D Printing: Since 3D printed parts, especially polymers, can exhibit anisotropy and layer adhesion weaknesses, designing with a safety margin under yield strength is critical to avoid early failure or warping.
Tensile Strength: The Last Line of Defense
Role in Safety: Tensile strength is the ultimate stress limit before the part fractures.
Why it matters: It represents the maximum load a structure can bear before catastrophic failure.
In 3D Printing: Understanding tensile strength helps engineers set maximum allowable loads and design parts to avoid fracture due to sudden impacts or unexpected overloads.
Safety Factors and Design Margins
Structural designs incorporate safety factors based on both yield and tensile strength.
Typical practice:
Design maximum expected loads to be well below the yield strength (e.g., 50–70%) to ensure no plastic deformation occurs.
Use tensile strength to determine absolute failure limits, and keep loads well below to prevent sudden breaks.
Summary
Aspect | Yield Strength | Tensile Strength |
---|---|---|
Structural Safety Role | Prevent permanent deformation | Prevent fracture or breakage |
Design Implication | Maintain loads within elastic limit | Ensure failure loads are avoided |
Safety Factor Use | Primary basis for working stress | Basis for ultimate failure stress |
In structural applications of 3D printed parts, balancing these two strengths and understanding how printing processes affect them is key to creating safe, reliable components.
Yield Strength vs Tensile Strength in 3D Printed Metals
Here is a comparison table of Yield Strength vs Tensile Strength for common 3D printed metals, especially relevant for technologies like SLM (Selective Laser Melting) and DMLS (Direct Metal Laser Sintering):
Material | Yield Strength (MPa) | Tensile Strength (MPa) | *Strength Ratio (Tensile / Yield) | Notes |
---|---|---|---|---|
316L Stainless Steel | 450–500 | 600–650 | ~1.3 | Corrosion-resistant; suitable for medical and chemical parts |
17-4PH Stainless Steel | 950–1050 | 1100–1200 | ~1.15 | High strength; commonly used for load-bearing components |
Ti6Al4V Titanium Alloy | 880–950 | 1000–1100 | ~1.13 | Lightweight and strong; widely used in aerospace |
Inconel 625 | 400–450 | 830–930 | ~2.0+ | High heat and corrosion resistance; ideal for extreme environments |
AlSi10Mg Aluminum Alloy | 190–240 | 320–370 | ~1.6 | Great for lightweight parts in automotive and aerospace |
*Note:
A larger ratio indicates that the material can continue to withstand significantly more stress after yielding before it fractures, demonstrating greater plastic deformation capacity.
A ratio closer to 1 means the material is likely to fracture soon after yielding, offering less safety margin and behaving in a more brittle manner.
Key Takeaways:
Highest Yield Strength: 17-4PH Stainless Steel (950–1050 MPa) – ideal for high-load structural parts.
Highest Tensile Strength: 17-4PH and Ti6Al4V (≥1100 MPa) – suitable for strength-critical and high-performance applications.
Largest Strength Ratio (Most Ductile): Inconel 625 (2.0+) – can undergo more plastic deformation after yielding, great for extreme conditions.
Lowest Strength Ratio (More Brittle): 17-4PH (1.15) – minimal margin between yielding and breaking, ideal for precision parts.
Lightweight & Strong: AlSi10Mg – well-suited for weight-sensitive applications in automotive and aerospace.
Conclusion
Understanding yield strength and tensile strength is important for making safe and strong 3D printed parts. Yield strength shows when a part starts to permanently deform, while tensile strength is the maximum load before it breaks.
In 3D printing, materials, print direction, and finishing affect these strengths. Knowing the difference helps design parts that won’t fail and choose the best printing method. This knowledge helps create durable, reliable 3D printed components.
Try Unionfab Industrial Manufacturing Services to Enhance 3D Printed Part Performance
Unionfab, the overseas branch of Uniontech, is China’s largest 3D printing manufacturer with 60% market share. With over 20 years of experience, 1,000+ industrial printers, and 6 advanced factories, Unionfab delivers high-quality, affordable 3D printing services.
We provide 80+ materials and technologies like SLA, SLM, SLS, MJF, FDM, DLP, and PolyJet—often at prices up to 70% lower than competitors.
Additionally, we offer CNC machining, vacuum casting, injection molding, and finishing for a complete manufacturing solution.
If you haven’t used Unionfab’s services above yet, sign up now to get a 10% discount on your first order!
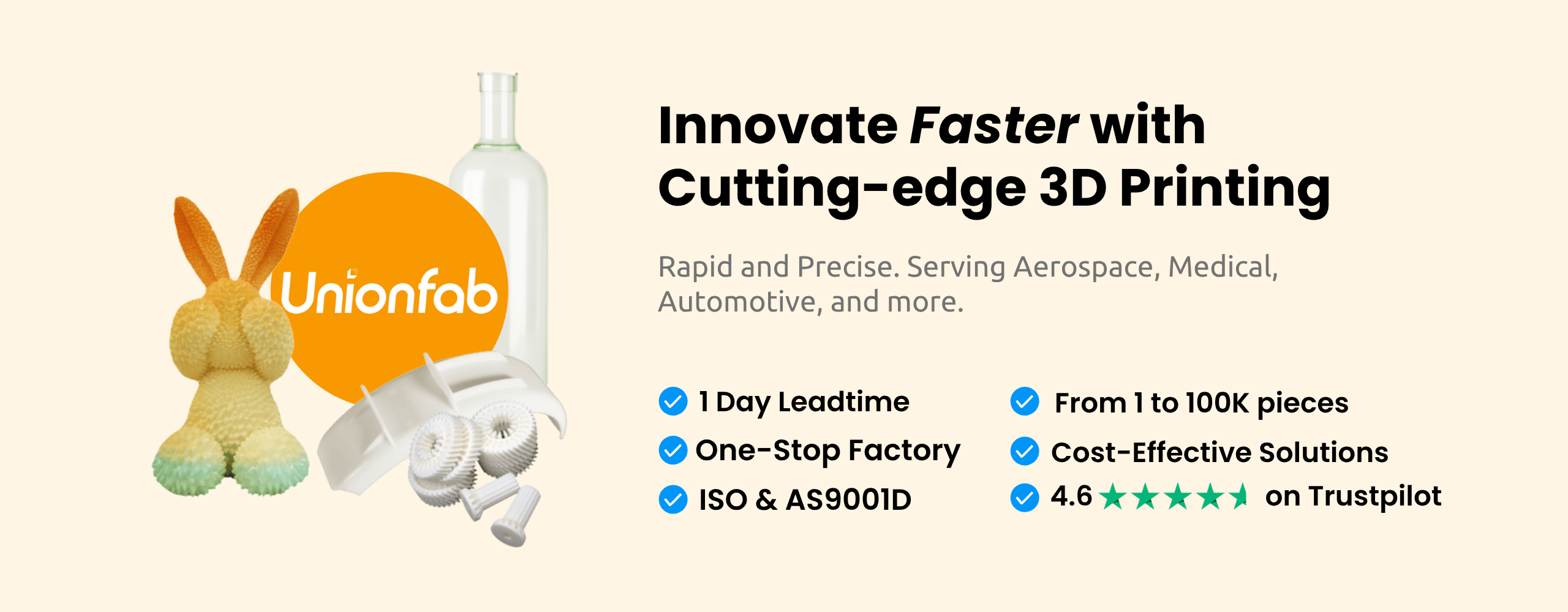
FAQs
Q1: Can 3D printed parts achieve the same yield and tensile strengths as traditionally manufactured parts?
A: It depends on the material and process. Metal 3D printing (e.g., SLM, DMLS) can produce parts with comparable strengths to traditional methods, while polymer prints generally have lower strength and anisotropy due to layer adhesion.
Q2: How does print orientation affect yield and tensile strength in 3D printing?
A: Layer orientation significantly impacts strength. Parts printed with layers aligned perpendicular to the load direction often have lower interlayer bonding strength, reducing both yield and tensile strength.
Q3: Should I design 3D printed parts based on yield strength or tensile strength?
A: Typically, design loads should stay well below the yield strength to avoid permanent deformation, using tensile strength as a limit to prevent catastrophic failure.