Guide to Aluminum 3D Printing[+Cost Calculator]
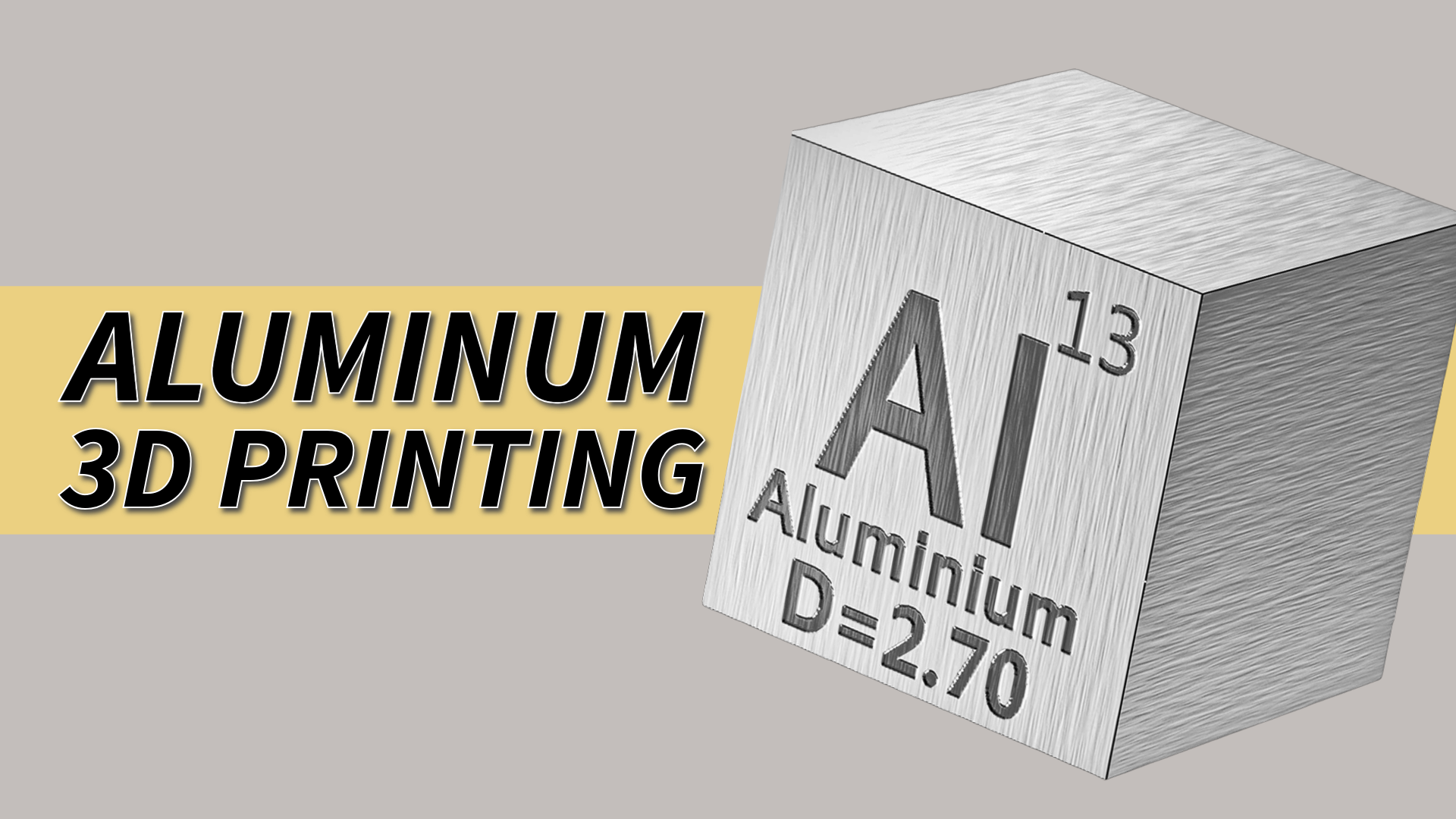
Discover a real success story of aluminum 3D printing and the edges of aluminum over other metals in 3D printing.
Introduction
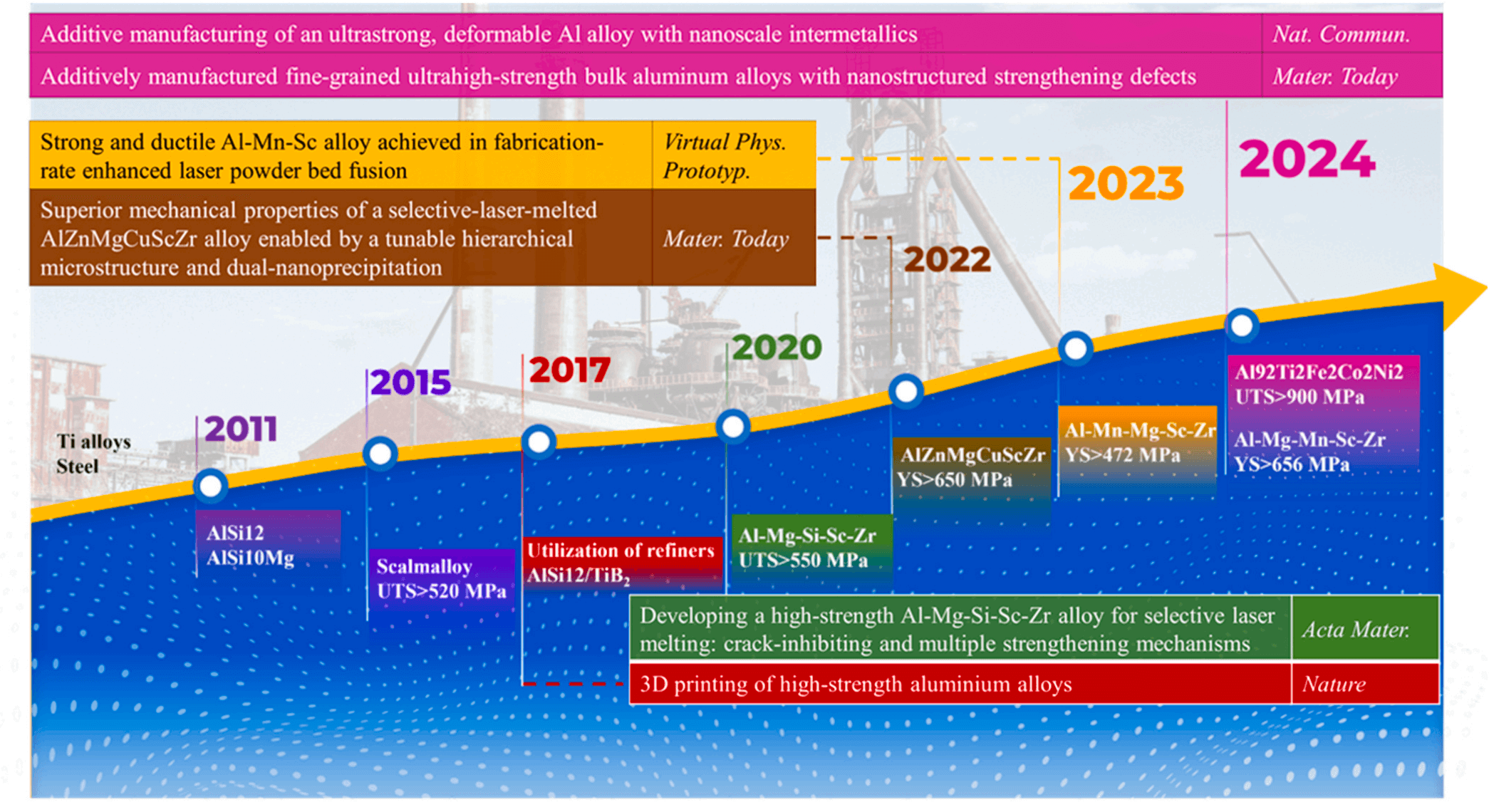
Source: https://doi.org/10.1016/j.msea.2024.147464
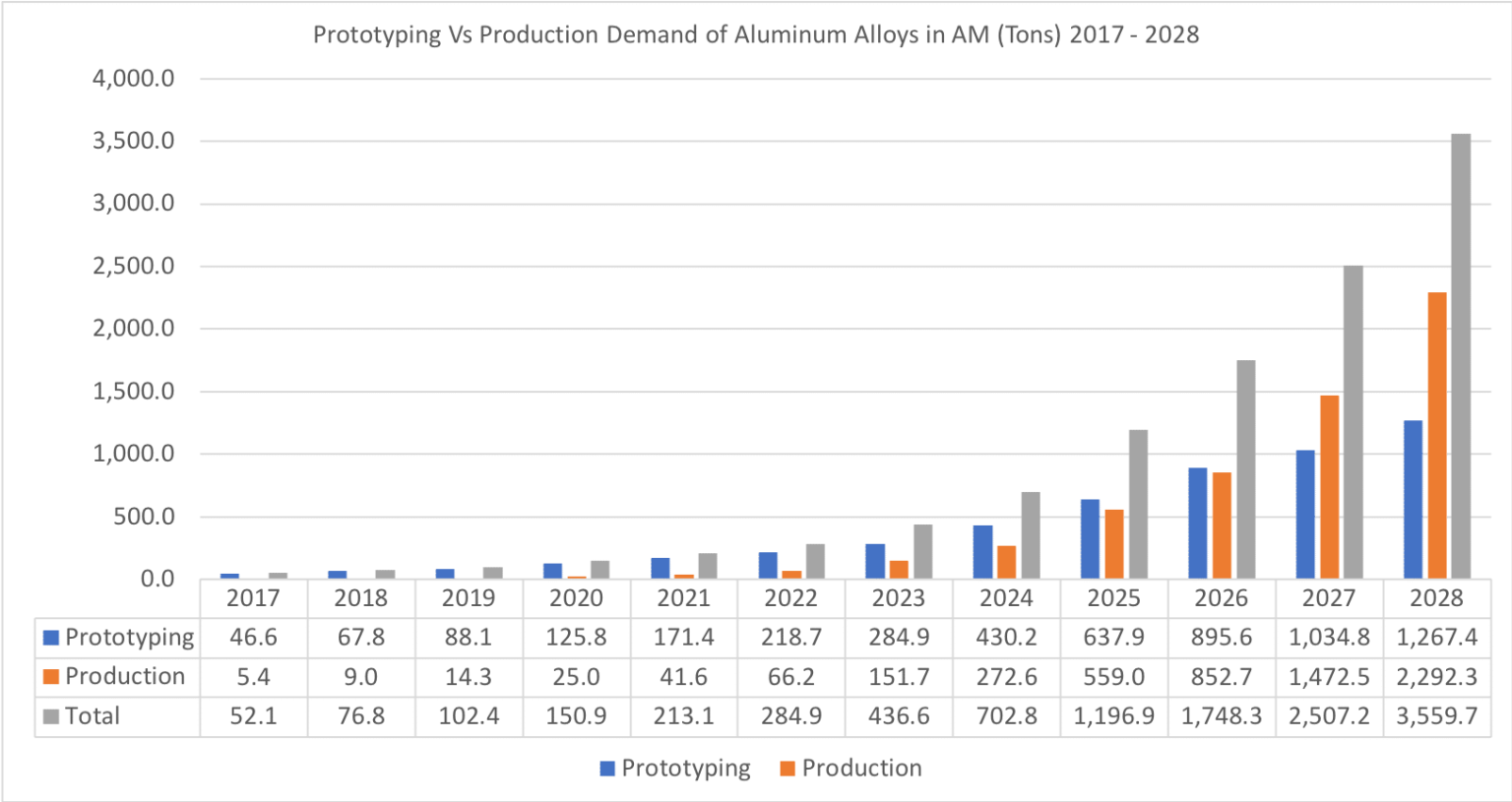
The initial application of aluminum in 3d printing can be traced to the year of 2011, when 3D printing was primarily used for polymers.
Whilst its adoption is relatively slower compared with that of steels and titanium alloys, significant progress has been made in the development of novel processes, alloys, and applications in the past 15 years around.
SmarTech Publishing (somewhat conservatively) once expected aluminum AM part production to overtake prototyping by 2027.
Unionfab’s Success Story of Aluminum 3D Printing in Aerospace
One of the wide applications of aluminum 3d printing to produce end parts is in aerospace. We, Unionfab, have recently helped an aerospace client out via utilizing this technology. The following is some background information.
Client Background
The client is an innovator in developing advanced plenums for aircraft engines. They planned to develop a high-performance engine plenum that would:
Optimize airflow for better engine performance.
Reduce weight without sacrificing strength.
Ensure durability in harsh aviation conditions.
Solution
Unionfab offered a solution combining sheet metal fabrication and SLM 3D printing with AlSi10Mg to manufacture the engine plenums.
Material Selection: Aluminum alloy was chosen over plastic for its perfect balance of strength, weight, and durability. It ensures reliability in harsh aviation conditions while being cost-effective for production.
Stringent Aerospace Standards: The parts were produced by Unionfab’s AS9100D-certified team, meeting the rigorous demands of the aerospace and defense industries.
Precise 3D Printing: The intricate geometries required for the plenums and injector pipes were achieved with Unionfab’s cutting-edge SLM 3D printing technology.
Result
The collaboration delivered exceptional results. To ensure a perfect fit, Unionfab also provided a free assembly test.
Enhanced Performance: The 3D-printed plenum optimized airflow, improving the engine’s efficiency and reliability.
Durability & Weight Reduction: AlSi10Mg maintained strength while reducing weight by 1–2 kg.
Fast Turnaround: Parts were manufactured and delivered within two weeks, meeting critical deadlines.
Eco-Friendly Manufacturing: 3D printing minimized material waste, aligning with Unicorn Aviation’s sustainability goals.
The success of this collaboration was largely due to aluminum alloy’s cost-effective strength-to-weight ratio. With a 30% higher strength-to-weight ratio than stainless steel and 50–70% lower cost than titanium, AlSi10Mg became our top choice.
So, what sets aluminum alloys apart from other common 3D printing metals?
Aluminum vs. Titanium vs. Steel vs. Copper vs. Nickle vs. Cobalt
In 3D printing, alloys outperform pure metals, which is why almost all 3D printing metals are alloys. Below, we’ve summarized and compared the performance of common 3D printing metal alloys to help you choose the most suitable material.
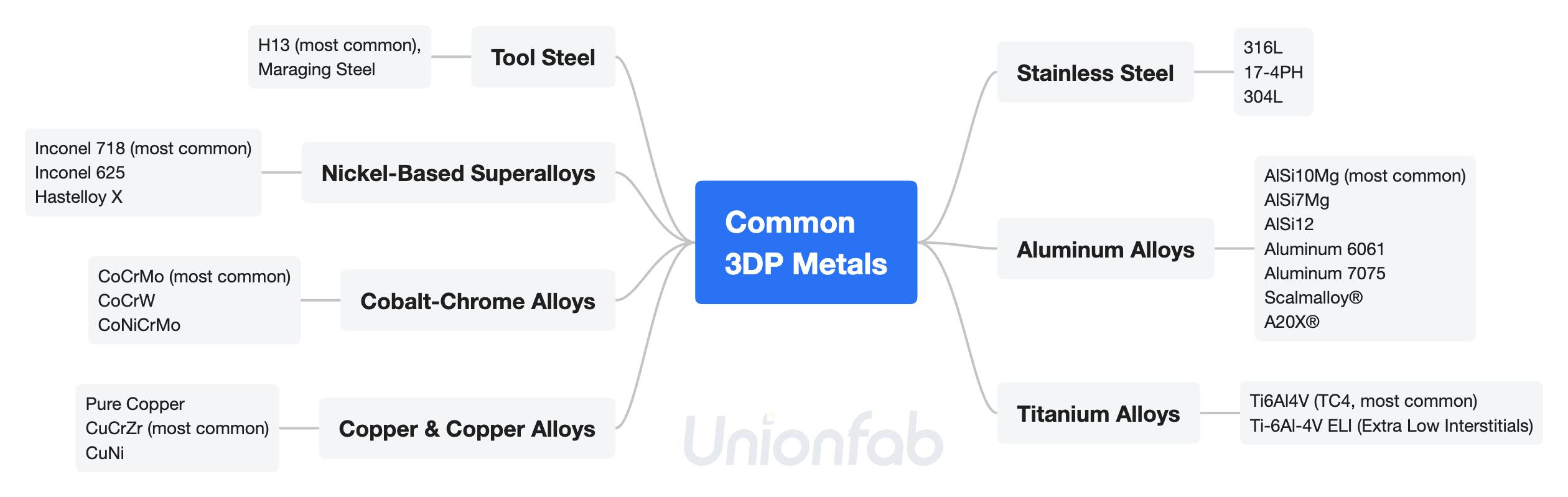
Material | Strength-to-Weight Ratio (MPa·g/cm³) | Corrosion Resistance (MPY) | Thermal Conductivity (W/m·K) | High-Temperature Resistance (°C) | Printability | Cost ($/kg) | Common Types Used in 3DP | Applications |
---|---|---|---|---|---|---|---|---|
Aluminum Alloys | 100-150 | 0.1-5.0 | 120-220 | 150-300 | 8 | 3-6 | AlSi10Mg (most common), AlSi12, 6061 Aluminum | Aerospace, automotive, industrial parts, lightweight structures |
Titanium Alloys | 200-260 | 0.01-0.5 | 6-12 | 400-600 | 6 | 30-80 | Ti6Al4V (most common), Ti-6Al-4V ELI (Extra Low Interstitials) | Aerospace, medical implants, high-performance automotive parts |
Stainless Steel | 80-120 | 0.1-1.0 | 15-25 | 600-800 | 5 | 5-12 | 316L Stainless Steel (most common), 17-4PH, 15-5PH, 304L | Industrial tools, automotive, aerospace, medical devices |
Tool Steel | 150-200 | 5-20 (coating needed) | 20-40 | 200-500 | 4 | 8-15 | H13 (most common), D2, M2, S7 | Tooling, dies, molds, manufacturing equipment |
Nickel-Based Superalloys | 180-220 | 0.01-0.1 | 10-15 | 800-1200 | 3 | 80-150 | Inconel 718 (most common), Inconel 625, Hastelloy X | High-temperature applications (e.g., jet engines, turbines, power plants) |
Cobalt-Chrome Alloys | 200-250 | 0.05-0.5 | 12-20 | 800-1100 | 4 | 100-200 | CoCrMo (most common), CoCrW, CoNiCrMo | Medical implants, aerospace, dental crowns and bridges |
Copper & Copper Alloys | 50-80 | 0.5-2.0 | 300-400 | 200-300 | 7 | 8-12 | Pure Copper, | Heat exchangers, electrical components, thermal management systems |
Material Recommendations:
Lightweight & Strength (aerospace, automotive):
Aluminum Alloys: Great strength-to-weight ratio, cost-effective.
Titanium Alloys: High strength, low weight for performance-critical parts.
High-Temperature Resistance (turbines, engines):
Nickel-Based Superalloys: Perfect for extreme high-temp environments.
Cobalt-Chrome Alloys: Ideal for high-temp, high-strength applications.
Corrosion Resistance (marine, chemical environments):
Titanium Alloys: Excellent corrosion resistance.
Stainless Steel: Good corrosion resistance for various industries.
Cost-Effective for High-Volume Production:
Aluminum Alloys: Affordable, easy to print for large-scale production.
Stainless Steel: Balanced cost and performance.
Precision & Durability (tools, medical, aerospace):
Stainless Steel: Durable and precise for medical devices and tools.
Tool Steel: Best for wear-resistant tools and molds.
To learn more about 3d printing metals, read the articles: Stainless Steel 3d printing, Titanium 3d printing, Copper 3d printing, Inconel 3d printing.
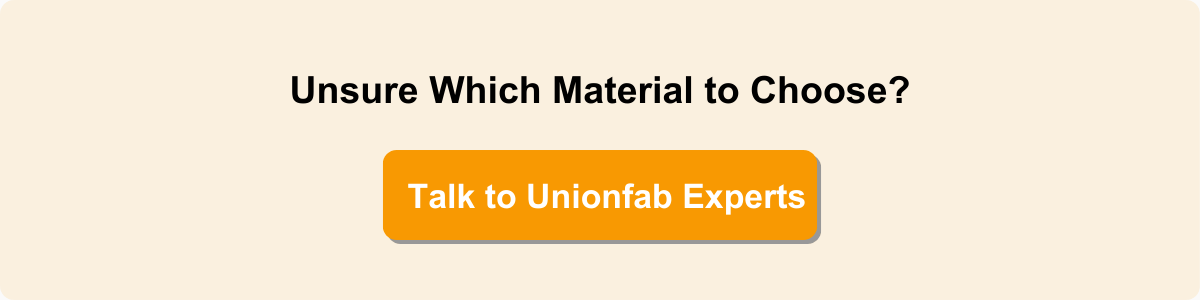
Comparison of Aluminum 3D Printing Service Providers
Here we have compared key global aluminum 3d printing service providers to help you choose the most suitable partner.
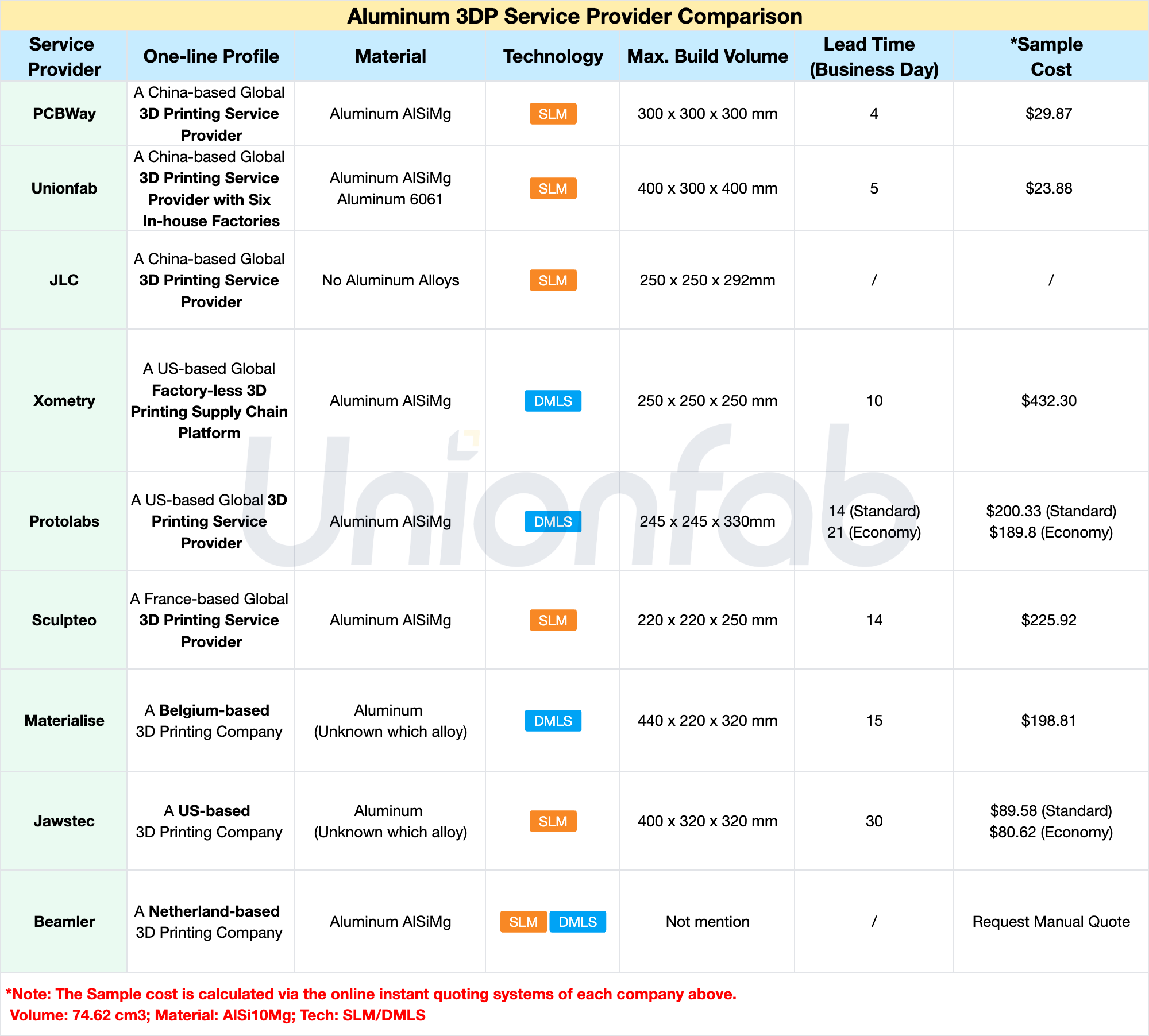
Aluminum 3D Printing Service Provider Recommendation
For Low Cost and Fast Turnaround: PCBWay (faster) and Unionfab (lower cost) are the best choices.
For Large Parts: Unionfab (affordable and fast), Materialise (higher cost and longer lead time) and Jawstec (longest lead time) stand out with larger build volumes.
Real Customer Feedback on Trustpilot
Below is the score of some companies above on Trustpilot. You can click the score to see feedback from real customers.
Service Provider | Xometry | Unionfab | Jawstec | PCBWay | Protolabs | Sculpteo | Materialise | JLC | Beamler |
---|---|---|---|---|---|---|---|---|---|
Trustpilot Score |
If you are in need of aluminum 3d printing service now, welcome to use Unionfab’s online free cost calculator to predict how much your print will cost.
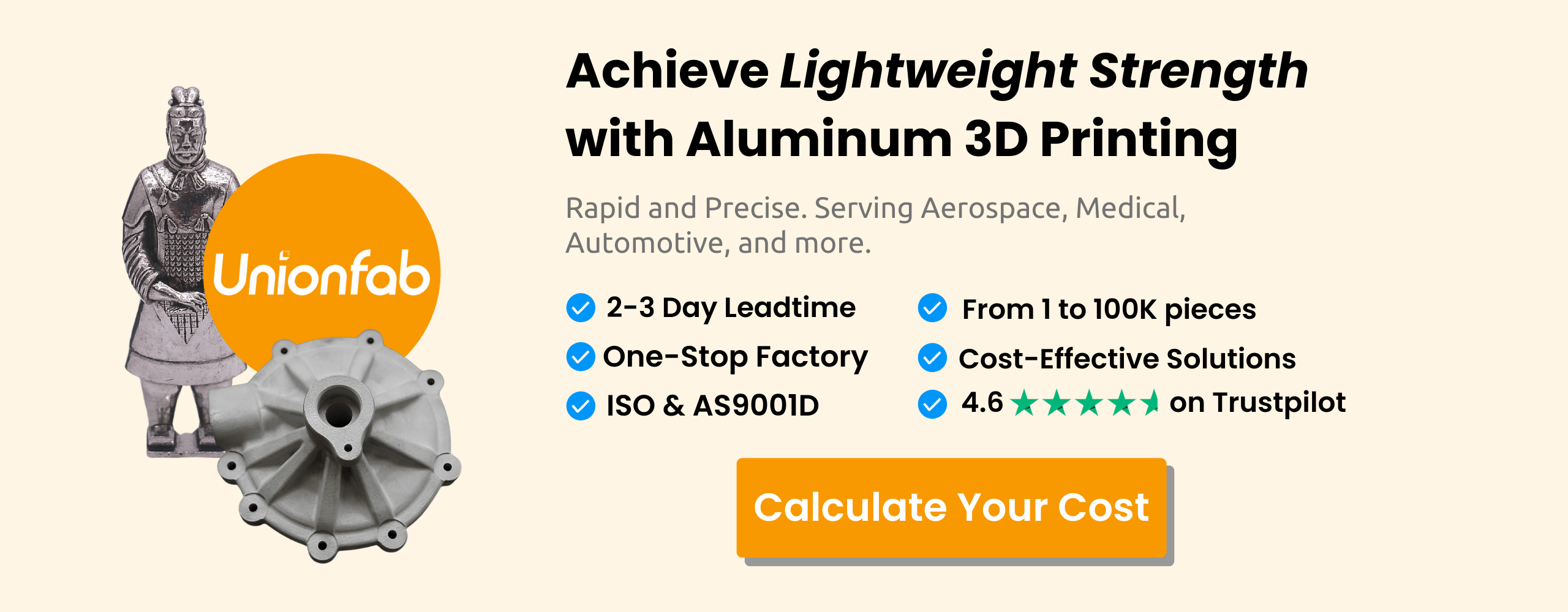
Unionfab’s Aluminum 3D Printing Service
The followings are the details of Unionfab’s aluminum 3d printing service.
SLM/DMLS | |
---|---|
Equipment | BLT; SLM; EOS; EXONE |
Materials | Aluminum (Alsi10Mg) |
Max Part Size | 400 x 300 x 400mm |
Layer Thickness | 0.035 mm |
Tolerance | ±0.2 mm |
Min. Wall Thickness | 0.5 mm |
*Min. Reference Unit Price | Aluminum (Alsi10Mg): |
Pass Rate | 99.5% |
Lead Time | As fast as 4-5 days |
On-time Delivery Rate | 98% |
Certification | ISO 9001, ISO 13485, and AS 9001D |
*The actual unit price is subject to real-time inquiry. |
If you haven’t used Unionfab’s 3d printing service yet, sign up now to get a 10% discount on your first order!
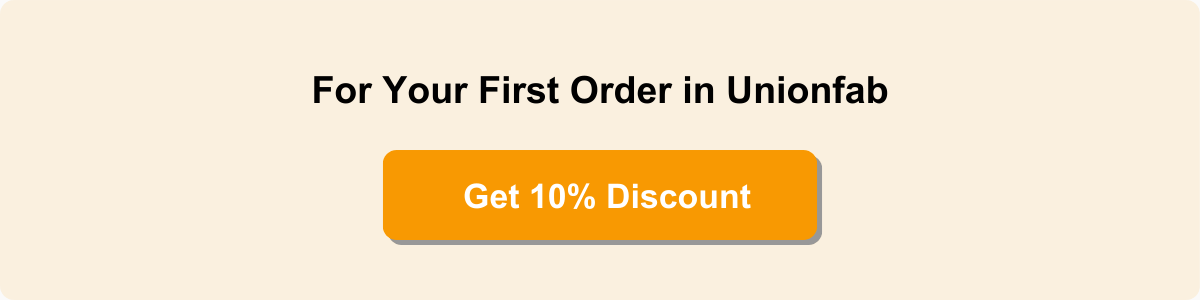
Post Processing
We not only provide high-precision printing but also a range of post-processing options below, including sandblasting, electroplating, and polishing etc., to improve surface quality, durability, and aesthetics of the prints, ensuring the perfect fit for various applications.
![]() | ![]() | ![]() | ![]() | ![]() |
---|---|---|---|---|
![]() | ![]() | ![]() | ![]() | ![]() |
![]() | ![]() | ![]() | ![]() | ![]() |
QA Report & Free Sample Printing
In addition to delivering cost-effective prints, we also offer quality assurance services and can send the QA report with the shipment.
For large-volume orders, free sample printing can be provided to ensure the final parts meet your specifications and quality standards before full production.
Technologies for Aluminum 3D Printing
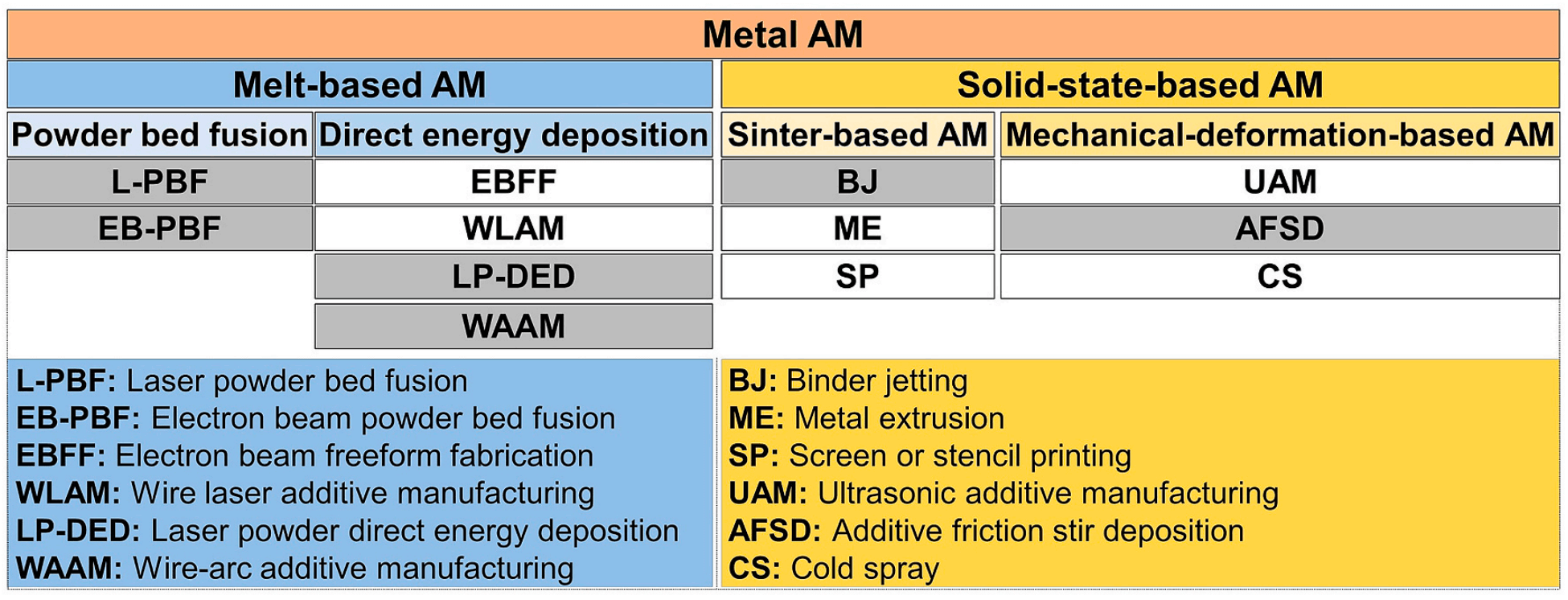
Source: https://doi.org/10.1016/j.ijmachtools.2023.104047
Among all the metal AM techniques above, 6 of them can be utilized to fabricate Al alloys: L-PBF, EB-PBF, LP-DED, WAAM, BJ(potential technique to be widely applied) and AFSD.
Among the 6 techniques, L-PBF is the most commonly used. So, we will mainly focus on L-PBF here. If you’re interested in other metal AM techniques, read our previous article on metal 3d printing, where all techniques are explained in detail.
L-PBF
L-PBF (Laser Powder Bed Fusion) is essentially another term for SLM (Selective Laser Melting), or DMLS (Direct Metal Laser Sintering). It uses a laser to selectively melt and fuse metal powder, layer by layer, to build up a solid part. The video below shows how the technique works.
For more details about L-PBF, or SLM 3d printing, read our previous article Guide to SLM 3D Printing/Metal LPBF [+Cost Calculator] to have a better understanding.
Different Types of Aluminum Alloys in 3D Printing
Aluminum alloys are typically divided into cast and wrought types, based on their manufacturing processes. The former dominated the initial employment of aluminum in 3D printing.
As research progressed, a wider variety of alloys have been used. Elements like Sc, Zr, and Mn have been added to improve alloy structures. The following table has compared the common available aluminum alloys used in 3d printing.
Alloy Type | Main Composition | 3D Printing Suitability | Strength | Heat Resistance (≈℃) | Wear Resistance | Corrosion Resistance |
---|---|---|---|---|---|---|
AlSi7Mg | 7% Si, 0.3% Mg | ✅ Suitable | 320/170 | ~200 | ★★☆☆☆ | ★★★★☆ |
AlSi10Mg | 10% Si, 0.3% Mg | ✅ Most commonly used | 400/250 | ~250 | ★★★☆☆ | ★★★★☆ |
AlSi12 | 12% Si | ✅ Suitable | 280/160 | ~250 | ★★★★☆ | ★★★☆☆ |
AlSi9Cu3 | 9% Si, 3% Cu | ⚠ Challenging | 320/200 | ~300 | ★★★☆☆ | ★★☆☆☆ |
Aluminum 6061 | 1% Mg, 0.6% Si | ⚠ Requires optimization | 310/275 (T6) | ~400 | ★★★☆☆ | ★★★☆☆ |
Aluminum 7075 | 5.6% Zn, 2.5% Mg, 1.6% Cu | ❌ Very difficult | 560/480 (T6) | ~450 | ★★★★☆ | ★★☆☆☆ |
Scalmalloy® | Al-Mg-Sc (0.7% Sc) | ✅ Designed for 3D printing | 520/480 | ~350 | ★★★☆☆ | ★★★★☆ |
A20X® | Al-Cu-Mg-Ag-Ti | ✅ Designed for 3D printing | 500/440 | ~400 | ★★★☆☆ | ★★★☆☆ |
In Summary,
✅ Best 3D Printing Options
General-purpose 3D printing: AlSi10Mg (most widely used, balanced printability and mechanical properties).
High-strength 3D printing: Scalmalloy® (superior strength and corrosion resistance, ideal for aerospace).
High-temperature applications: A20X® (excellent heat resistance and high strength).
⚠ Feasible but Requires Optimization
AlSi9Cu3 (requires preheating and optimized laser parameters).
6061 (requires specialized powders and high-temperature preheating).
❌ Not Recommended
7075 (extremely prone to cracking, very difficult to 3D print).
If you need high strength, Scalmalloy or A20X is the best choice. For general engineering applications, AlSi10Mg remains the most practical option.
For detailed properties of the most popular AlSi10Mg, download the datasheet below.
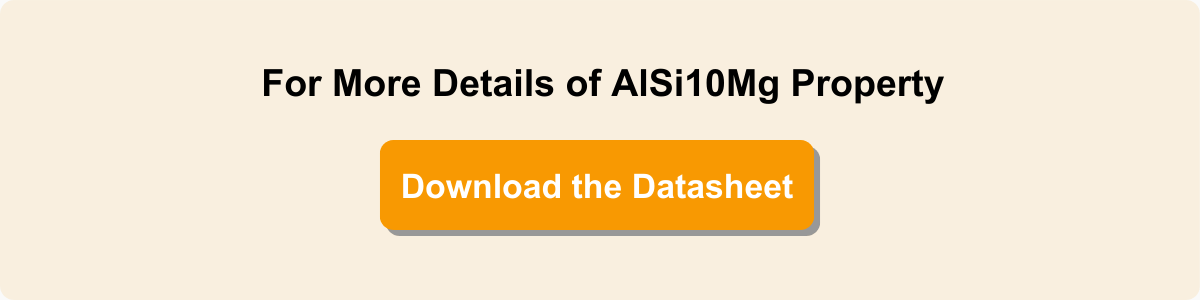
Defects of Aluminum Alloys in 3D Printing and Solutions
Defects:
Certain defects can arise during the printing process due to the material’s behavior under heat and pressure.
Porosity
Cause: During printing, aluminum absorbs hydrogen, which forms small gas pockets as the material cools. This happens because aluminum tends to trap gas at high temperatures, leading to tiny holes inside the solid part.
Impact: Porosity weakens the material, reducing its strength and fatigue resistance.
Cracking
Cause: Rapid heating and cooling during printing create thermal stress, which can cause cracks, especially in high-strength alloys like 6061 and 7075.
Impact: Cracking lowers the part’s overall strength and makes it more likely to fail under pressure.
Oxidation
Cause: Aluminum forms an oxide layer when exposed to oxygen, which prevents proper fusion during printing. This oxide layer is tough and has a higher melting point than aluminum.
Impact: Oxidation leads to poor bonding between layers, resulting in weak spots and reduced material strength.
Lack of Fusion
Cause: Aluminum alloys are highly reflective, causing the laser to lose energy and fail to melt the powder properly. This leads to incomplete bonding between layers.
Impact: Incomplete fusion results in weak points and poor layer adhesion, weakening the part.
Warping and Residual Stresses
Cause: Aluminum cools quickly, creating thermal gradients that cause parts to warp or distort during or after printing.
Impact: This can result in dimensional inaccuracies and weakened structural integrity.
Design Strategies to Minimize Defects in 3D Printing
Increase Strength and Stability
Increase wall thickness to avoid thin walls and reduce porosity.
Use lattice or honeycomb structures to reduce thermal stress and lower the risk of warping and cracking.
Optimize Geometry
Avoid sharp corners: use rounded transitions to reduce stress concentration and prevent cracking.
Avoid large flat areas: use ribs or lattice structures to distribute thermal stress and reduce cracking and warping.
Design with symmetry to ensure even cooling and reduce deformation or stress concentration caused by asymmetry.
Improve Contact and Fusion
Increase contact area between layers: ensure large contact surfaces to promote better fusion and avoid narrow or shallow connections.
Optimize infill design to prevent sealed cavities, reducing the risk of trapped gases.
Reduce Oxidation and Lack of Fusion
Reduce thin features and increase wall thickness in delicate areas to improve stability and avoid oxidation.
Avoid unsupported features: minimize structures requiring excessive support to ensure key joints are free from oxidation.
Optimize Support Structures
When unavoidable, add proper support to ensure part stability and reduce deformation or warping during printing.
Distribute support points evenly, especially at the bottom, to prevent warping and deformation.
Applications Across Industries
Aerospace and Defense
Aluminum 3D printing enhances aerospace and defense by creating lightweight components that improve fuel efficiency and payload capacity. It enables complex geometries for aerodynamic and functional advantages, while customization supports specialized applications like UAVs and satellites.
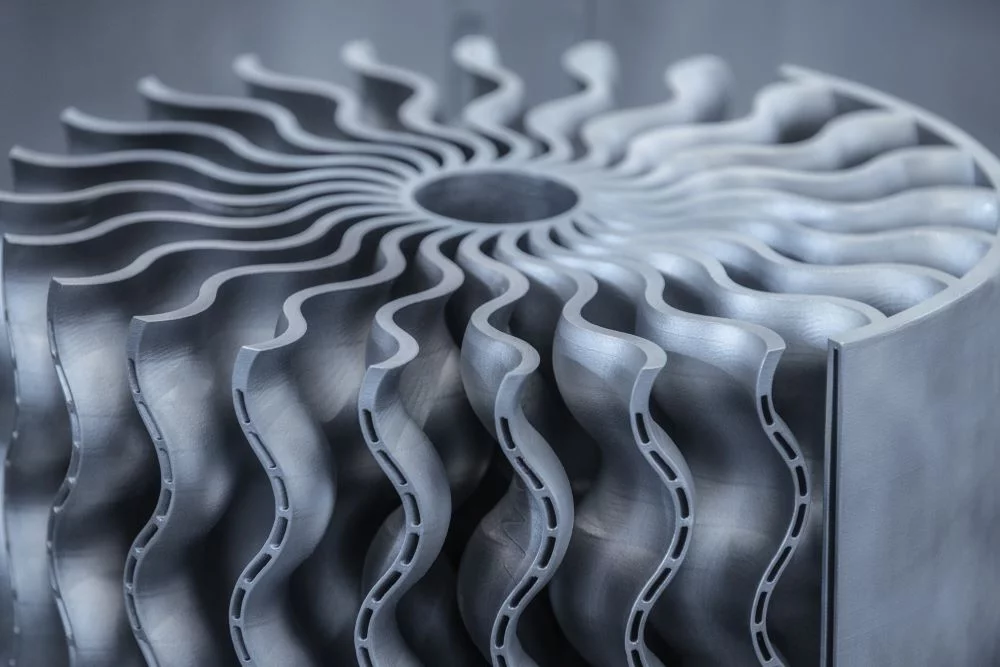
Source: images.squarespace-cdn.com
Automotive
In automotive, aluminum 3D printing advances lightweighting with parts that boost vehicle performance and fuel efficiency. It speeds up prototyping and allows for customized components like heat exchangers for electric vehicles, enhancing sustainability and product innovation.
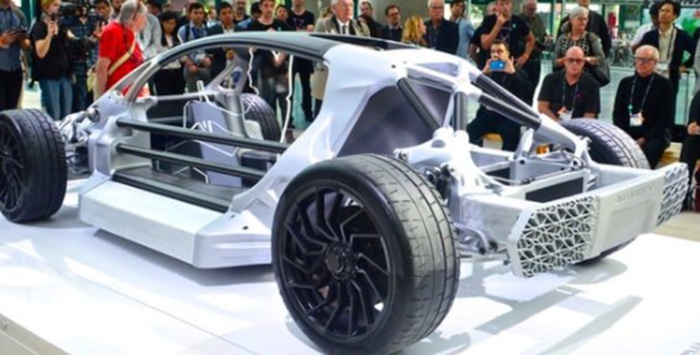
Source: eplus3d.com
Medical and Healthcare
For medical applications, aluminum 3D printing produces custom implants and surgical tools tailored to patient anatomy, improving comfort and precision. It also develops durable medical devices meeting rigorous standards, such as braces and orthotics, enhancing patient care and treatment options.
Consumer Goods and Electronics
In consumer goods and electronics, aluminum 3D printing designs high-performance products like heat sinks with optimized thermal management. It enables customized consumer products and accelerates prototyping, fostering innovation in design and functionality across various applications.
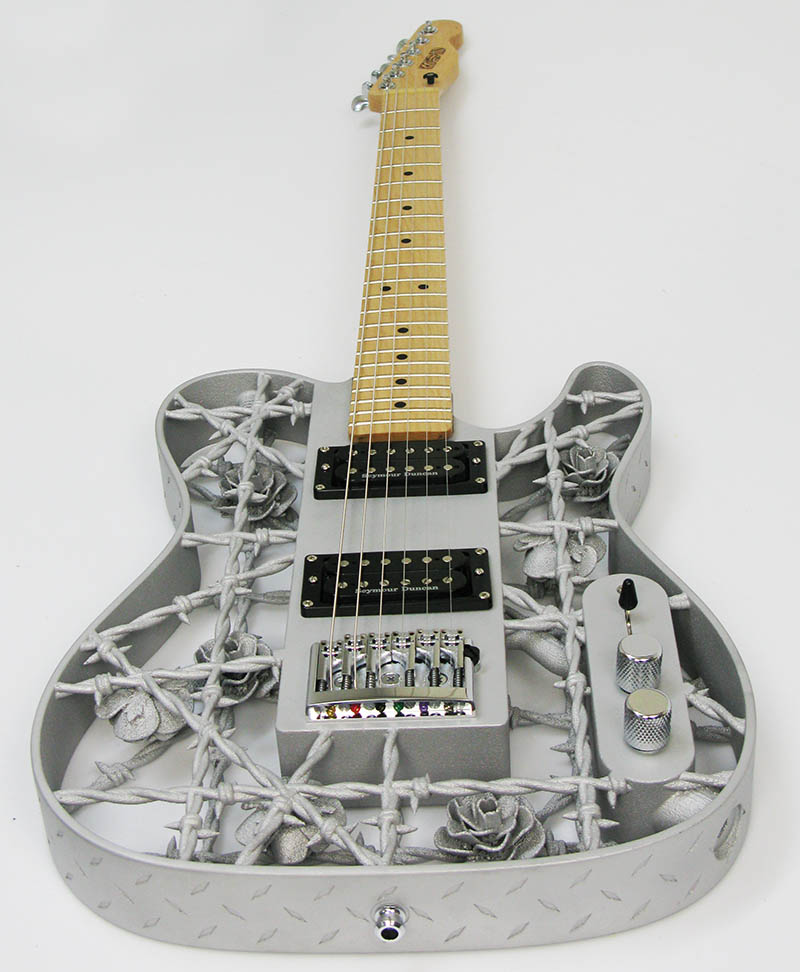
Source: 3dprintingindustry.com
Conclusion
Aluminum 3D printing offers revolutionary capabilities in design flexibility, cost efficiency, and sustainability, despite challenges like material variability and regulatory complexities.
Advancements in materials and processes continue to expand its applications, promising to redefine industry standards and drive innovation globally.